Abstract
Modern machining processes are now focused on machinability aspects of brittle and hard to machine materials. As per concerns raised in the field of machinability of brittle materials, the prime obstacle in the process is their hardness. Such car** issues can be suppressed through a bit increase in softness of the brittle materials. Therefore, heating of such material can raise the bar for the softness in such materials so as to their machinability. But the localized heating leads to a higher temperature gradient between heated and non-heated regions of the work material so as the thermal stresses in it which results into micro- as well as macro-cracks. Such deplorable issues can be solved through bulk heating of the work materials. Apparently, the comparisons of their softness can be examined through the scratch tests performed at different temperatures. In the view of above elucidation, 45S5 bioglass samples have been used for micro scratch tests as well as a portable heating setup is used to heat those samples. The temperature values are kept between room temperature (27 ℃) and 420 ℃ during the performed tests. Subsequently, traction force, coefficient of friction during the scratch tests and scratch images are compared as the elucidated outcome softness of the material. It is found that there is a significant reduction in traction forces and coefficient of frictions during tests with rise in the sample temperature.
Access this chapter
Tax calculation will be finalised at checkout
Purchases are for personal use only
Similar content being viewed by others
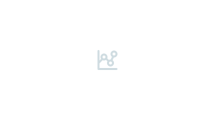
References
Le Bourhis E, Metayer D (2000) Indentation of glass as a function of temperature. J Non-Crystalline Solids 34–38
Manshadi ST (2009) Laser assisted machining of inconel 718 superalloy. McGill University Montréal.
Lei S, Shin YC, Incropera FP (2001) Experimental investigation of thermo-mechanical characteristics in laser-assisted machining of silicon nitride ceramics. J Manuf Sci Eng 123(4):639–646
Rebro PA, Shin YC, Incropera FP (2004) Design of operating conditions for crackfree laser-assisted machining of mullite. Int J Mach Tools Manuf 44(7–8):677–694
Jeon Y, Park HW, Lee CM (2013) Current research trends in external energy assisted machining. Int J Precis Eng Manuf 14(2):337–342
Lei S, Shin YC, Incropera FP (2000) Deformation mechanisms and constitutive modeling for silicon nitride undergoing laser-assisted machining. Int J Mach Tools Manuf 40(15):2213–2233
Rebro PA, Shin YC, Incropera FP (2002) Laser-assisted machining of reaction sintered mullite ceramics. J Manuf Sci Eng 124(4):875–885
Chang C-W, Kuo C-P (2007) Evaluation of surface roughness in laser-assisted machining of aluminum oxide ceramics with Taguchi method. Int J Mach Tools Manuf 47(1):141–147
George C (1991) Laser machining—theory and practice. Springer, New York
Chryssolouris G et al (1988) Theoretical aspects of a laser machine tool
Haferkamp H, Seebaum D (1994) Material removal on tool steel using high power CO2-lasers. In: Proceedings of the conference on laser assisted net shape engineering (LANE′ 94)., Meisenbach, Bamberg
Hench LL et al (1971) Bonding mechanisms at the interface of ceramic prosthetic materials. J Biomed Mater Res 5(6):117–141
Hench LL (2013) Chronology of bioactive glass development and clinical applications
Thompson ID, Hench LL (1998) Mechanical properties of bioactive glasses, glass-ceramics and composites. Proc Inst Mech Eng [H] 212(2):127–136
Briscoe BJ, Pelillo E, Sinha SK (1996) Scratch hardness and deformation maps for polycarbonate and polyethylene. Polym Eng Sci 36(24):2996–3005
Narasimman P, Pushpavanam M, Periasamy V (2012) Wear and scratch resistance characteristics of electrodeposited nickel-nano and micro SiC composites. Wear 292:197–206
Varga M et al (2017) Study of wear mechanisms at high temperature scratch testing. Wear 388:112–118
Pazhanivel B, Kumar TP, Sozhan G (2015) Machinability and scratch wear resistance of carbon-coated WC inserts. Mater Sci Eng, B 193:146–152
Wang N et al (2019) Research on the machinability of A-plane sapphire under diamond wire sawing in different sawing directions. Ceram Int 45(8):10310–10320
Zhang Z et al (2010) Nanoscale machinability and subsurface damage machined by CMP of soft-brittle CdZnTe crystals. Int J Adv Manuf Technol 47(9–12):1105–1112
Zhang S et al (2015) Structural optimisation and synthesis of multilayers and nanocomposite AlCrTiSiN coatings for excellent machinability. Surf Coat Technol 277:23–29
Tseng AA et al (2009) Scratching properties of nickel-iron thin film and silicon using atomic force microscopy. J Appl Phys 106(4):044314
Da Silva L et al (2020) Critical assessment of compacted graphite cast iron machinability in the milling process. J Manuf Process 56:63–74
Singh JK, Rao US, Pyare R (2020) Design and development of a multipurpose portable heating setup for 45S5 bioglass and other ceramic samples. Rev Sci Instrum 91(10):105108
Author information
Authors and Affiliations
Corresponding author
Editor information
Editors and Affiliations
Rights and permissions
Copyright information
© 2023 The Author(s), under exclusive license to Springer Nature Singapore Pte Ltd.
About this paper
Cite this paper
Singh, J.K., Rao, U.S., Pyare, R. (2023). Study of Traction Forces at Elevated Temperatures During Micro-Scratch Tests on 45S5 Bioglass. In: Maurya, A., Srivastava, A.K., Jha, P.K., Pandey, S.M. (eds) Recent Trends in Mechanical Engineering. Lecture Notes in Mechanical Engineering. Springer, Singapore. https://doi.org/10.1007/978-981-19-7709-1_57
Download citation
DOI: https://doi.org/10.1007/978-981-19-7709-1_57
Published:
Publisher Name: Springer, Singapore
Print ISBN: 978-981-19-7708-4
Online ISBN: 978-981-19-7709-1
eBook Packages: EngineeringEngineering (R0)