Abstract
This paper proposes a novel dynamic impulse forming technology, that is, laser shock hydraulic warm free-bulging. This technology is especially suitable for low-plasticity but temperature-sensitive metal materials. Laser shock hydraulic warm free-bulging can tremendously increase the formability of materials and is often used in sheet metal forming fields. Thus, this technology expends the application area of laser shock liquid forming. In this study, AZ31B magnesium alloy foils with a thickness of 90 μm were investigated in room temperature to 393 K and in the laser energy range of 450–810 mJ. Maximal forming heights were obtained at different temperatures. Results showed that the maximal forming height of AZ31B magnesium alloy improved markedly as the temperature increased. Furthermore, the free-bulging height reached the maximum of 324.4 μm at 363 K. The height increased approximately 18% compared with that at room temperature. When the temperature exceeded 363 K, the maximal forming height decreased. Then, the microhardness and thinning ratio of the formed parts were investigated. At 363 K, the thinning ratio was also the largest, while the formed parts maintained a fine microhardness. Finally, through electron backscattered diffraction (EBSD) technology, the dynamic recrystallisation mechanisms and texture evolution of the formed parts at different temperatures were investigated to determine for the deformation mechanism at various temperatures. At 363 K, many fine grains and twins were obtained, improving the formability. Meanwhile, the dislocation density increased and became more uniform as the temperature increased and reached a peak at 363 K, resulting in maximal microhardness.

















Similar content being viewed by others
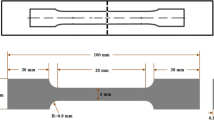
Data availability
Not applicable.
Code availability
Not applicable.
References
Irthiea I, Green G, Hashim S, Kriama A (2014) Experimental and numerical investigation on micro deep drawing process of stainless steel 304 foil using flexible tools. Int J Mach Tool Manu 76:21–33. https://doi.org/10.1016/j.ijmachtools.2013.09.006
Fu MW, Chan WL (2013) A review on the state-of-the-art microforming technologies. Int J Adv Manuf Technol 67:2411–2437. https://doi.org/10.1007/s00170-012-4661-7
Mai JM, Peng LF, Lai XM, Lin ZQ (2013) Electrical-assisted embossing process for fabrication of micro-channels on 316L stainless steel plate. J Mater Process Technol 213(2):314–321. https://doi.org/10.1016/j.jmatprotec.2012.09.013
Choudhary V (2013) MEMS: fundamental technology and applications. CRC Press, Boca Raton
Zhao QJ, Wang CJ, Yu HP, Guo B, Shan DB, Li CF (2011) Micro bulging of thin T2 copper sheet by electromagnetic forming. Trans Nonferrous Metal Soc 21:461–464. https://doi.org/10.1016/S1003-6326(11)61625-7
Psyk V, Risch D, Kinsey BL, Tekkaya AE, Kleiner M (2011) Electromagnetic forming—a review. J Mater Process Technol 211(5):787–829. https://doi.org/10.1016/j.jmatprotec.2010.12.012
Golovashchenko SF, Gillard AJ, Mamutov AV (2013) Formability of dual phase steels in electrohydraulic forming. J Mater Process Technol 213(7):1191–1212. https://doi.org/10.1016/j.jmatprotec.2013.01.026
Mynors DJ, Zhang B (2002) Applications and capabilities of explosive forming. J Mater Process Technol 125–126:1–25. https://doi.org/10.1016/S0924-0136(02)00413-2
Liu HX, Shen ZB, Wang X, Wang HJ, Tao MK (2010) Micromould based laser shock embossing of thin metal sheets for MEMS applications. Appl Surf Sci 256(14):4687–4691. https://doi.org/10.1016/j.apsusc.2010.02.073
Feng F, Huang SY, Meng ZH, Hu JH, Lei Y, Zhou MC, Wu D, Yang ZZ (2014) Experimental study on tensile property of AZ31B magnesium alloy at different high strain rates and temperatures. Mater Des 57:10–20. https://doi.org/10.1016/j.matdes.2013.12.031
Hu XY, Daehn GS (1996) Effect of velocity on flow localization in tension. Acta Mater 44(3):1021–1033. https://doi.org/10.1016/1359-6454(95)00228-6
Follansbee PS, Gray GT III (1991) Dynamic deformation of shock prestrained copper. Mater Sci Eng A 138(1):23–31. https://doi.org/10.1016/0921-5093(91)90673-B
Cheng GJ, Pirzada D, Ming Z (2007) Microstructure and mechanical property characterizations of metal foil after microscale laser dynamic forming. J Appl Phys 101:063108. https://doi.org/10.1063/1.2710334
Zheng C, Sun S, Ji Z, Wang W, Liu J (2010) Numerical simulation and experimentation of micro scale laser bulge forming. Int J Mach Tool Manuf 50(12):1048–1056. https://doi.org/10.1016/j.ijmachtools.2010.08.012
Ma Y, Xu Y, Zhang SH, Banabic D, El-Aty AA, Chen DY, Cheng M, Song HW, Pokrovsky AI, Chen GQ (2018) Investigation on formability enhancement of 5A06 aluminium sheet by impact hydroforming. CIRP Ann Manuf Technol 67(1):281–284. https://doi.org/10.1016/j.cirp.2018.04.024
Niaraki RJ, Fazli A, Soltanpour M (2019) Electromagnetically activated high-speed hydroforming process: a novel process to overcome the limitations of the electromagnetic forming process. CIRP J Manuf Sci Technol 27:21–30. https://doi.org/10.1016/j.cirpj.2019.09.002
Woo MA, Noh HG, An WJ, Song WJ, Kang BS, Kim J (2017) Numerical study on electrohydraulic forming process to reduce the bouncing effect in electromagnetic forming. Int J Adv Manuf Technol 89:1813–1825. https://doi.org/10.1007/s00170-016-9230-z
Samardzic V, Geskin ES, Atanov GA, Semko AN, Kovaliov A (2008) Investigation of liquid impact-based macro-, meso- and microforming processes. J Mater Eng Perform 17:302–315. https://doi.org/10.1007/s11665-008-9230-8
Je G, Malka D, Kim H, Hong S, Shin B (2017) A study on micro hydroforming using shock wave of 355 nm UV-pulsed laser. Appl Surf Sci 417:244–249. https://doi.org/10.1016/j.apsusc.2017.02.146
Liu HX, Liu F, Ma YJ, Jiang CK, Wang X (2018) Investigation of a novel laser shock liquid flexible microforming process applied to embossing three-dimensional large area microarrays on metallic foils. Int J Adv Manuf Technol 99:419–435. https://doi.org/10.1007/s00170-018-2453-4
He YC, Liu HX, Ma YJ, Yan Z, Wang X (2022) Numerical and experimental investigation of laser shock microhydroforming technology for microforming thin-walled LA103Z alloy foil with complex microfeatures. J Manuf Process 73:290–305. https://doi.org/10.1016/j.jmapro.2021.11.024
El-Magd E, Abouridouane M (2006) Characterization, modelling and simulation of deformation and fracture behaviour of the light-weight wrought alloys under high strain rate loading. Int J Impact Eng 32(5):741–758. https://doi.org/10.1016/j.ijimpeng.2005.03.008
Li QZ (2012) Mechanical properties and microscopic deformation mechanism of polycrystalline magnesium under high-strain-rate compressive loadings. Mater Sci Eng A 540:130–134. https://doi.org/10.1016/j.msea.2012.01.116
Friedrich H, Schumann S (2001) Research for a “ new age of magnesium” in the automotive industry. J Mater Process Technol 117(3):276–281. https://doi.org/10.1016/S0924-0136(01)00780-4
Mukai T, Watanabe H, Higashi K (2000) Application of superplasticity in commercial magnesium alloy for fabrication of structural components. Mater Sci Technol Lond 16(11–12):1314–1319. https://doi.org/10.1179/026708300101507163
Barnett MR, Stanford N, Cizek P, Beer A, Xuebin Z, Keshavarz Z (2009) Deformation mechanisms in mg alloys and the challenge of extending room-temperature plasticity. JOM 61:19–24. https://doi.org/10.1007/s11837-009-0115-6
Staroselsky A, Anand L (2003) A constitutive model for hcp materials deforming by slip and twinning: application to magnesium alloy AZ31B. Int J Plast 19(10):1843–1864. https://doi.org/10.1016/S0749-6419(03)00039-1
Luan J, Sun C, Li X, Zhang Q (2014) Constitutive model for AZ31 magnesium alloy based on isothermal compression test. Mater Sci Technol Lond 30(2):211–219. https://doi.org/10.1179/1743284713Y.0000000341
Hou QY, Wang JT (2010) A modified Johnson-Cook constitutive model for Mg-Gd-Y alloy extended to a wide range of temperatures. Comp Mater Sci 50(1):147–152. https://doi.org/10.1016/j.commatsci.2010.07.018
Sanjari M, Farzadfar SA, Jung IH, Essadiqi E, Yue S (2012) Influence of strain rate on hot deformation behaviour and texture evolution of AZ31B. Mater Sci Technol Lond 28(4):437–447. https://doi.org/10.1179/1743284711Y.0000000080
Agnew SR, Duygulu O (2005) Plastic anisotropy and the role of non-basal slip in magnesium alloy AZ31B. Int J Plast 21(6):1161–1193. https://doi.org/10.1016/j.ijplas.2004.05.018
Al-Samman T, Gottstein G (2008) Dynamic recrystallization during high temperature deformation of magnesium. Mater Sci Eng A 490(1–2):411–420. https://doi.org/10.1016/j.msea.2008.02.004
Lee BH, Bang W, Ahn S, Lee CS (2008) Effects of temperature and strain rate on the high-temperature workability of strip-cast Mg-3Al-1Zn alloy. Metall Mater Trans A 39A(6):1426–1434. https://doi.org/10.1007/s11661-008-9515-4
Barnett MR (2001) Influence of deformation conditions and texture on the high temperature flow stress of magnesium AZ31. J Light Metals 1(3):167–177. https://doi.org/10.1016/S1471-5317(01)00010-4
Zhang SH, Xu YC, Palumbo G, Pinto S, Tricarico L, Wang ZT, Zhang QL (2005) Formability and process conditions of magnesium alloy sheets. Mater Sci Forum 488–489:453–456. https://doi.org/10.4028/www.scientific.net/MSF.488-489.453
Ren LM, Zhang SH, Palumbo G, Tricarico L (2008) Warm deep drawing of magnesium alloy sheets — formability and process conditions. Proc Inst Mech Eng B J Eng 222(11):1347–1354. https://doi.org/10.1243/09544054JEM1114
Sepahi-Boroujeni S, Fereshteh-Saniee F (2015) The influences of the expansion equal channel angular extrusion operation on the strength and ductility of AZ80 magnesium alloy. Mater Sci Eng A 636:249–253. https://doi.org/10.1016/j.msea.2015.03.073
Li YS, Qu C, Wang JH, Xu R (2020) Exceptional aging hardening behaviour of nanocrystalline Mg-Y-Nd-Gd-Zr alloy prepared by high pressure torsion. J Alloy Compd 813:152123. https://doi.org/10.1016/j.jallcom.2019.152123
Galiyev A, Sitdikov O, Kaibyshev R (2003) Deformation behavior and controlling mechanisms for plastic flow of magnesium and magnesium alloy. Mater Trans 44(4):426–435. https://doi.org/10.2320/matertrans.44.426
Funding
This work is supported by the National Natural Science Foundation of China (grant no. 52075226) and the Innovation Practice Fund of Jiangsu University Industrial Centre (grant no. ZXJG2021008).
Author information
Authors and Affiliations
Contributions
Zhang Yan: conceptualisation, methodology, data curation, investigation, writing—original draft preparation. Youjuan Ma: validation, writing and editing, resources. Huixia Liu: supervision, visualisation, funding acquisition. **ao Wang: project administration, formal analysis.
Corresponding author
Ethics declarations
Ethics approval
Not applicable.
Consent to participate
There is no consent to participate needed in the present study.
Consent for publication
The authors consent to publish.
Competing interests
The authors declare no competing interests.
Additional information
Publisher's note
Springer Nature remains neutral with regard to jurisdictional claims in published maps and institutional affiliations.
Rights and permissions
Springer Nature or its licensor (e.g. a society or other partner) holds exclusive rights to this article under a publishing agreement with the author(s) or other rightsholder(s); author self-archiving of the accepted manuscript version of this article is solely governed by the terms of such publishing agreement and applicable law.
About this article
Cite this article
Yan, Z., Ma, Y., Liu, H. et al. Investigation on formability and mechanism in laser shock hydraulic warm free-bulging of AZ31B magnesium alloy foils. Int J Adv Manuf Technol 126, 505–517 (2023). https://doi.org/10.1007/s00170-023-11143-4
Received:
Accepted:
Published:
Issue Date:
DOI: https://doi.org/10.1007/s00170-023-11143-4