Abstract
This work proposes a thermodynamic-based constitutive model for shape memory alloy, which captures the gradual variation in stress–strain response from the shape memory effect to the pseudoelastic effect. The present model also provides a framework for modeling various other responses, such as strain temperature hysteresis and thermally induced strain recovery effect. The model classifies the different phases of the material, such as twinned martensite, detwinned martensite, and austenite, and the mix of these phases using only two internal variables, namely austenite volume fraction and inelastic martensite strain. The proposed model shows that introducing two independent yield conditions corresponding to each internal variable is sufficient to describe all the phase transformations. After presenting the theoretical framework of the model, the procedure for numerical implementation has been discussed. The simulation shows the gradual variation in the stress–strain curve at different temperatures in the phase transformation range and is observed to have an adequate quantitative agreement with the experimental data The model is further implemented for different shape memory alloys to show the possibility of the generalized framework for this class of materials. In addition, the capability of simulating other phenomena of SMA, such as strain response for thermal loading at constant stress and the complete response of strain recovery in shape memory behavior, is also presented.













Similar content being viewed by others
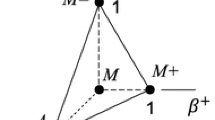
References
Saburi T 1998 Ti-Ni shape memory alloys. In: Shape memory materials, pp. 49–96
Duerig T W, Melton K N, and Stöckel D 2013 Engineering Aspects of Shape Memory Alloys Butterworth-Heinemann,
Jani J M, Leary M, Subic A and Gibson M A 2014 A review of shape memory alloy research, applications and opportunities. Mater. Design 56: 1078–1113
Lorenza Petrini and Francesco Migliavacca 2011 Biomedical applications of shape memory alloys. J. Metall. 2011: e501483
Jeya Ganesh N, Maniprakash S, Chandrasekaran L, Srinivasan S M, and Srinivasa A R 2011 Design and development of a sun tracking mechanism using the direct SMA actuation J. Mech. Design, 133(7)
Saeed Akbari Amir, Hosein Sakhaei, Sahil Panjwani, Kavin Kowsari and Qi Ge 2021 Shape memory alloy based 3D printed composite actuators with variable stiffness and large reversible deformation. Sens. Actuators A: Phys. 321: 112598
Ali Hussein F M, Manan Khan Abdul, Hangyeol Baek, Buhyun Shin and Youngshik Kim 2021 Modeling and control of a finger-like mechanism using bending shape memory alloys. Microsyst. Technol. 27(6): 2481–2492
Fares Maimani, Calderón Ariel A, **ufeng Yang, Alberto Rigo, Ge Joey Z and Pérez-Arancibia Néstor O 2022 A 7-mg miniature catalytic-combustion engine for millimeter-scale robotic actuation. Sens. Actuators A: Phys. 341: 112818
Mohammadreza Lalegani Dezaki, Mahdi Bodaghi, Ahmad Serjouei, Shukri Afazov and Ali Zolfagharian 2022 Adaptive reversible composite-based shape memory alloy soft actuators. Sens. Actuators A: Phys. 345: 113779
Cheikh Cisse, Wael Zaki and Tarak Ben Zineb 2016 A review of constitutive models and modeling techniques for shape memory alloys. Int. J. Plast. 76: 244–284
Ashish Khandelwal and Vidyashankar Buravalla 2009 Models for shape memory alloy behavior: an overview of modeling approaches. Int. J. Struct. Changes Solids 1(1): 111–148
Alberto Paiva and Amorim Savi Marcelo 2006 An overview of constitutive models for shape memory alloys. Math. Probl. Eng. 2006: e56876
Kikuaki Tanaka, Shigenori Kobayashi and Yoshio Sato 1986 Thermomechanics of transformation pseudoelasticity and shape memory effect in alloys. Int. J. Plast. 2(1): 59–72
Liang C and Rogers C A 1990 One-dimensional thermomechanical constitutive relations for shape memory materials. J, Intell. Mater. Syst. Struct. 8(4): 285–302
Brinson L C 1993 One-dimensional constitutive behavior of shape memory alloys: thermomechanical derivation with non-constant material functions and redefined martensite internal variable: J. Intell. Mater. Syst. Struct.
Banerjee A 2012 Simulation of shape memory alloy wire actuator behavior under arbitrary thermo-mechanical loading. Smart Mater. Struct. 21(12): 125018
Jarali Chetan S, Chikkangoudar Ravishankar N, Patil Subhas F, Raja S, Lu Charles Y, and Fish Jacob 2019 Thermodynamically consistent approach for one-dimensional phenomenological modeling of shape memory alloys Int. J. Multiscale Comput. Eng., 17(4)
Arthur Adeodato, Vignoli Lucas L, Alberto Paiva, Monteiro Luciana L S, Pacheco Pedro M C L and Savi Marcelo A 2022 A shape memory alloy constitutive model with polynomial phase transformation kinetics. Shape Memory Superelasticity 8(4): 277–294
Auricchio F and Lubliner J 1997 A uniaxial model for shape-memory alloys. Int. J. Solids Struct. 34(27): 3601–3618
Panoskaltsis V P, Bahuguna S and Soldatos D 2004 On the thermomechanical modeling of shape memory alloys. Int. J. Non-Linear Mech. 39(5): 709–722
Souza Angela C, Mamiya Edgar N and Nestor Zouain 1998 Three-dimensional model for solids undergoing stress-induced phase transformations. Eur. J. Mech. A/Solids 17(5): 789–806
Ferdinando Auricchio and Lorenza Petrini 2004 A three-dimensional model describing stress-temperature induced solid phase transformations: solution algorithm and boundary value problems. Int. J. Numerical Methods Eng. 61(6): 807–836
Boyd J G and Lagoudas D C 1996 A thermodynamical constitutive model for shape memory materials Part I. The monolithic shape memory alloy. Int. J. Plast. 12(6): 805–842
Qidwai M A and Lagoudas D C 2000 On thermomechanics and transformation surfaces of polycrystalline NiTi shape memory alloy material. Int. J. Plast. 16(10): 1309–1343
Peter Popov and Lagoudas Dimitris C 2007 A 3-D constitutive model for shape memory alloys incorporating pseudoelasticity and detwinning of self-accommodated martensite. Int. J. Plast. 23(10–11): 1679–1720
Auricchio F, Bonetti E, Scalet G and Ubertini F 2014 Theoretical and numerical modeling of shape memory alloys accounting for multiple phase transformations and martensite reorientation. Int. J. Plast. 59: 30–54
Zhixiang Rao, Jiaming Leng, Zehong Yan, Limeng Tan and **aojun Yan 2023 A three-dimensional constitutive model for shape memory alloy considering transformation-induced plasticity, two-way shape memory effect, plastic yield and tension-compression asymmetry. Eur. J. Mech. A/Solids 99: 104945
Dimitris Chatziathanasiou, Yves Chemisky, George Chatzigeorgiou and Fodil Meraghni 2016 Modeling of coupled phase transformation and reorientation in shape memory alloys under non-proportional thermomechanical loading. Int. J. Plast. 82: 192–224
Guillaume Helbert, Luc Saint-Sulpice, Shabnam Arbab Chirani, Lamine Dieng, Thibaut Lecompte, Sylvain Calloch and Philippe Pilvin 2014 Experimental characterisation of three-phase NiTi wires under tension. Mech. Mater. 79: 85–101
Frost M, Jury A, Heller L and Sedlák P 2021 Experimentally validated constitutive model for NiTi-based shape memory alloys featuring intermediate R-phase transformation: A case study of Ni48Ti49Fe3. Mater. Design 203: 109593
Longfei Wang, Peihua Feng, Xuegang **ng, Ying Wu and Zishun Liu 2021 A one-dimensional constitutive model for NiTi shape memory alloys considering inelastic strains caused by the R-phase transformation. J. Alloys Compd. 868: 159192
Jan Frenzel 2020 On the importance of structural and functional fatigue in shape memory technology. Shape Memory Superelasticity 6(2): 213–222
Dornelas Vanderson M, Oliveira Sergio A, Savi Marcelo A, Lopes Pacheco Pedro Manuel Calas and Souza de Luis Felipe G 2021 Fatigue on shape memory alloys: experimental observations and constitutive modeling. Int. J. Solids Struct. 213: 1–24
Woodworth Lucas A, Felix Lohse, Karl Kopelmann, Chokri Cherif and Michael Kaliske 2022 Development of a constitutive model considering functional fatigue and pre-stretch in shape memory alloy wires. Int. J. Solids Struct. 234–235: 111242
Alsawalhi Mohammed Y and Landis Chad M 2022 A new phenomenological constitutive model for shape memory alloys. Int. J. Solids Struct. 257: 111264
Grabe C and Bruhns O T 2008 On the viscous and strain rate dependent behavior of polycrystalline NiTi. Int. J. Solids Struct. 45(7): 1876–1895
Claire Morin, Ziad Moumni and Wael Zaki 2011 Thermomechanical coupling in shape memory alloys under cyclic loadings: Experimental analysis and constitutive modeling. Int. J. Plast. 27(12): 1959–1980
Mingzhao Zhuo 2020 Timescale competition dictates thermo-mechanical responses of niti shape memory alloy bars. Int. J. Solids Struct. 193–194: 601–617
Hartl Darren J, George Chatzigeorgiou and Lagoudas Dimitris G 2010 Three-dimensional modeling and numerical analysis of rate-dependent irrecoverable deformation in shape memory alloys. Int. J. Plast. 26(10): 1485–1507
Ashwin Rao, Annie Ruimi and Srinivasa Arun R 2014 Internal loops in superelastic shape memory alloy wires under torsion—experiments and simulations/predictions. Int. J. Solids Struct. 51(25): 4554–4571
Viet N V, Zaki W, Umer R and Xu Y 2020 Mathematical model for superelastic shape memory alloy springs with large spring index. Int. J. Solids Struct. 185–186: 159–169
Hamid Khodaei and Patrick Terriault 2018 Experimental validation of shape memory material model implemented in commercial finite element software under multiaxial loading. J. Intell. Mater. Syst. Struct. 29(14): 2954–2965
Nallathambi Ashok K, Doraiswamy Srikrishna, Chandrasekar A S and Srinivasan Sivakumar M 2009 A 3-species model for shape memory alloys. Int. J. Struct. Changes Solids 1(1): 149–170
Karakalas A, Machairas T, Solomou A, and Saravanos D 2017 Effect of shape memory alloy partial transformation on the performance of morphing wind turbine airfoils. In: 28th International Conference on Adaptive Structures and Technologies, ICAST
Coleman Bernard D and Gurtin Morton E 1967 Thermodynamics with internal state variables. J. Chem. Phys. 47(2): 597–613
Klinkel S 2006 A phenomenological constitutive model for ferroelastic and ferroelectric hysteresis effects in ferroelectric ceramics. Int. J. Solids Struct. 43(22–23): 7197–7222
Miehe C and Rosato D 2011 A rate-dependent incremental variational formulation of ferroelectricity. Int. J Eng. Sci. 49(6): 466–496
Shaw John A and Stelios Kyriakides 1995 Thermomechanical aspects of NiTi. J. Mech. Phys. Solids 43(8): 1243–1281
Wu X D, Sun G J and Wu J S 2003 The nonlinear relationship between transformation strain and applied stress for nitinol. Mater. Lett. 57(7): 1334–1338
Sivom Manchiraju, Darrell Gaydosh, Othmane Benafan, Ronald Noebe, Raj Vaidyanathan and Anderson Peter M 2011 Thermal cycling and isothermal deformation response of polycrystalline NiTi: simulations versus experiment. Acta Materialia 59(13): 5238–5249
Ashrafi M J 2019 Constitutive modeling of shape memory alloys under cyclic loading considering permanent strain effects. Mech. Mater. 129: 148–158
Bingfei Liu, Shangyang **, Keying Chen, Fusheng Wang and Chunzhi Du 2019 Study on cyclic deformation behavior of shape memory alloy materials considering damage and the residual strain. J. Alloys Compd. 797: 1142–1150
Sittner P, Heller L, Pilch J, Sedlak P, Frost M, and Chemisky Y et al 2009 Roundrobin SMA modeling. In: ESOMAT 2009 - 8th European Symposium on Martensitic Transformations, p. 08001
Eisenwasser J D and Brown L C 1972 Pseudoelasticity and the strain-memory effect in Cu-Zn-Sn alloys. Metall. Trans. 3(6): 1359–1363
Saleeb A F, Dhakal B, Dilibal S, Owusu-Danquah J S and Padula S A 2015 On the modeling of the thermo-mechanical responses of four different classes of NiTi-based shape memory materials using a general multi-mechanism framework. Mech. Mater. 80: 67–86
Acknowledgements
This work was supported by a grant from Science and Engineering Research Board (SERB) under the SRG program, Project no.: SRG/2021/001672. The authors would also like to thank Dr.Ratna Kumar Annabattula from IITM Chennai for the fruitful discussions regarding this work.
Author information
Authors and Affiliations
Corresponding author
Rights and permissions
Springer Nature or its licensor (e.g. a society or other partner) holds exclusive rights to this article under a publishing agreement with the author(s) or other rightsholder(s); author self-archiving of the accepted manuscript version of this article is solely governed by the terms of such publishing agreement and applicable law.
About this article
Cite this article
Reddy, G.J., S, M. Quantitative modeling of the variation in stress–strain response of shape memory alloys in partial phase transformed state. Sādhanā 49, 114 (2024). https://doi.org/10.1007/s12046-024-02437-8
Received:
Revised:
Accepted:
Published:
DOI: https://doi.org/10.1007/s12046-024-02437-8