Abstract
Due to their unique advantages of high strength, high performance, and light weight, ultra-thin-walled (UTW) tubes have attracted increasing application in the aviation and aerospace industries. However, wrinkling, cracking, cross-section distortion, and even collapse easily occur in UTW tube bending process. In this study, a new mandrel design method with variation in the mandrel ball thickness for bending UTW tubes was proposed to improve the forming quality. First, a basic mandrel design scheme with a uniform mandrel ball thickness was determined according to engineering experiences and preliminary research. Then, three different mandrel ball thicknesses were determined based on the same mandrel support angle of the basic scheme (BS), and combination schemes (CSs) of mandrel balls with different thicknesses were designed. A 3D elastic–plastic finite element (FE) model of the numerical control (NC) bending process of UTW tubes was established and verified, and the influence of different combinations of mandrel ball thickness variation on the bending quality of UTW tubes was investigated. The results showed that compared with the BS, the CSs can effectively improve the von Mises stress distribution and wall thickness uniformity on the extrados, and significantly reduce the wall-thinning ratio, wall-thickening ratios, and ovality of the UTW bent tube. The combination scheme with as many thin mandrel balls as possible at the beginning of the bending and thick mandrel balls at the end of the support was beneficial to reduce the wall-thinning ratio. Increasing the number of medium or thick mandrel balls in combination scheme can increase the mandrel support angle and reduce the ovality of the UTW bent tubes. These results are of great significance for guiding the design of mandrels and improving the forming quality of UTW tubes.












Similar content being viewed by others
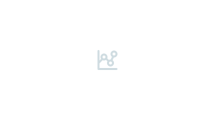
Availability of data
The authors confirm that the data supporting the findings of this study are available in this article.
References
Li H, Yang H, Yan J, Zhan M (2009) Numerical study on deformation behaviors of thin-walled tube NC bending with large diameter and small bending radius. Comp Mater Sci 45:921–934. https://doi.org/10.1016/j.commatsci.2008.12.018
Wang XS, Li F (2015) Analysis of wall thickness variation in the hydro-bending of a double-layered tube. Int J Adv Manuf Technol 81:67–72. https://doi.org/10.1007/s00170-015-7188-x
Groth S, Engel B, Langhammer K (2018) Algorithm for the quantitative description of freeform bend tubes produced by the three-roll-push-bending process. Prod Eng 12:517–524. https://doi.org/10.1007/s11740-018-0795-2
Guo XZ, Ma YN, Chen WL, **ong H, Xu Y, El-Aty AA, ** K (2018) Simulation and experimental research of the free bending process of a spatial tube. J Mater Process Techol 255:137–149. https://doi.org/10.1016/j.jmatprotec.2017.11.062
Yang H, Yan J, Zhan M, Li H, Kou Y (2009) 3D numerical study on wrinkling characteristics in NC bending of aluminum alloy thin-walled tubes with large diameters under multi-die constraints. Comp Mater Sci 45:1052–1067. https://doi.org/10.1016/j.commatsci.2009.01.010
Yan J, Yang H, Zhan M, Li H (2010) Forming limits under multi-index constraints in NC bending of aluminum alloy thin-walled tubes with large diameters. Sci China Techol Sc 53(2):326–342. https://doi.org/10.1007/s11431-009-0331-x
Liu N, Yang H, Li H, Tao ZJ, Hu X (2015) An imperfection-based perturbation method for plastic wrinkling prediction in tube bending under multi-die constraints. Int J Mech Sci 98:178–194. https://doi.org/10.1016/j.ijmecsci.2015.03.023
Li GJ, Yang H, Xu XD, Li H, Yang H (2018) Formability of thin-walled commercial pure titanium tube upon rotary draw bending. Rere Metal Mat Eng 47(1):26–32. https://doi.org/10.1016/S1875-5372(18)30066-3
Zhang JJ, Yang H, Zhan M, Shen SJ (2008) Effects of pressing die's boosting function on wall thinning and springback in NC bending process of thin-walled tube with large diameter. J Plast Eng 15(1):60−65. https://www.engineeringvillage.com/search/doc/abstract.url?&pageType=quickSearch&usageZone=resultslist&usageOrigin=searchresults&searchtype=Quick&SEARCHID=f8e136ead117424a8a46f98a8a3d65a4&DOCINDEX=1&ignore_docid=cpx_30c221118c7ac7dd4M7e0f2061377553&database=1&format=quickSearchAbstractFormat&tagscope=&displayPagination=yes. (in Chinese)
Jiang LF, Wang YQ, Lin YC, Zhang SY, Li H, Zhang F, Feng YX, Guo XZ (2020) Effect of mandrel parameters on NC RDB forming quality of ultra-thin-walled tube. J **’an Jiaotong Univ 54(4):144–154. https://doi.org/10.7652/xjtuxb202004018. (in Chinese)
** XY, Li HG, Ling J, Tao J (2015) Numerical simulation and experimental investigation on press-bending with internal pressure of ultra thin - wall tube of 6061 aluminum alloy. J Plast Eng 22(5):69–75. https://doi.org/10.3969/j.issn.1007-2012.2015.05.013. (in Chinese)
Li H, Yang H, Zhan M, Sun ZC, Gu RJ (2007) Role of mandrel in NC precision bending process of thin-walled tube. Int J Mach Tool Manu 47:1164–1175. https://doi.org/10.1016/j.ijmachtools.2006.09.001
Li C, Yang H, Zhan M, Xu XD, Li GJ (2009) Effects of process parameters on numerical control bending process for large diameter thin-walled aluminum alloy tubes. Nonferrous Met Soc China 19:668–673. https://doi.org/10.1016/S1003-6326(08)60331-3
Liu ZW, Dong FF, Li LX, Yao ZQ (2015) Process parameters optimization of rotary draw bending for large diameter thin-walled steel tube for automotive bumper. Auto Eng 37(7):853–860. https://doi.org/10.19562/j.chinasae.qcgc.2015.07.020
Safdarian R (2020) Investigation of tube fracture in the rotary draw bending process using experimental and numerical methods. Int J Mater Form 13:493–516. https://doi.org/10.1007/s12289-019-01484-5
Xu J, Yang H, Zhan M, Li H (2011) Design and optimisation of mandrel parameters for thin walled aluminum alloy tube NC bending. Mater Res Innov 15(sup 1):365–369. https://doi.org/10.1179/143307511X12858957674878
Li H, Xu J, Yang H, Yang H, Li GJ (2017) Sequential multi-objective optimization of thin-walled aluminum alloy tube bending under various uncertainties. Trans Nonferrous Met Soc China 27:608–615. https://doi.org/10.1016/S1003-6326(17)60068-2
Fang J, Lu SQ, Wang KL, Xu JM, Xu XM, Yao ZJ (2013) Effect of mandrel on cross-section quality in numerical control bending process of stainless steel 2169 small diameter tube. Adv Mater Sci Eng 849495:1–9. https://doi.org/10.1155/2013/849495
Ancellotti S, Benedetti M, Fontanari V, Slaghenaufi S, Tassan M (2016) Rotary draw bending of rectangular tubes using a novel parallelepiped elastic mandrel. Int J Adv Manuf Technol 85:1089–1103. https://doi.org/10.1007/s00170-015-8000-7
Xue X, Liao J, Vincze G, Gracio JJ (2016) Modelling of mandrel rotary draw bending for accurate twist springback prediction of an asymmetric thin-walled tube. J Mater Process Techol 216:405–417. https://doi.org/10.1016/j.jmatprotec.2014.10.007
Jiang LF, Lin WM, Wen DW, Liu H, Lu CD, Gu YQ (2015) A new bionic elastic mandrel for application in the spatial consecutive RDB with no straight line. JBBBE 25:12–18. https://doi.org/10.4028/www.scientific.net/JBBBE.25.12
Jiang LF, Zhang SY, Wang YQ, Feng YX, Lin YC, Liu H, Zhang F, Shao H (2019) Research on bending forming method of large diameter-thickness ratio thin-walled tubes for aerospace. Int J Adv Manuf Technol 102:3037–3049. https://doi.org/10.1007/s00170-019-03328-7
Funding
The work was supported by the Zhejiang Province Public Welfare Technology Application Research Project(LGG22E050027), the Open Foundation of the State Key Laboratory of Fluid Power and Mechatronic Systems (GZKF-202126), and the National Natural Science Foundation of China (Nos.U20A20287).
Author information
Authors and Affiliations
Contributions
Jiang LF conceived and designed the study; Wang YQ performed numerical simulation and analyzed the data; Lin YC performed the bending experiments; Sun M. edited the manuscript; Jiang LF, Li H., Zhang SY and Feng YX reviewed and improved the manuscript.
Corresponding author
Ethics declarations
Ethical approval
This study complies with the ethical standards set out by Springer.
Consent to participate
Not applicable.
Consent to publish
Not applicable.
Competing interests
The authors declare no competing interests.
Additional information
Publisher's Note
Springer Nature remains neutral with regard to jurisdictional claims in published maps and institutional affiliations.
Rights and permissions
Springer Nature or its licensor holds exclusive rights to this article under a publishing agreement with the author(s) or other rightsholder(s); author self-archiving of the accepted manuscript version of this article is solely governed by the terms of such publishing agreement and applicable law.
About this article
Cite this article
Jiang, L., Lin, Y., Li, H. et al. A new mandrel design with mandrel ball thickness variation for the bending process of aviation ultra-thin-walled tubes. Int J Adv Manuf Technol 122, 1805–1819 (2022). https://doi.org/10.1007/s00170-022-09954-y
Received:
Accepted:
Published:
Issue Date:
DOI: https://doi.org/10.1007/s00170-022-09954-y